Manufacturers Integrate Data from Multiple Systems to Increase Profits
Typically, when seeking to improve the bottom line, manufacturers consider increasing income/profits and decreasing costs. They may even think about increasing efficiency.
However, in this day and age, manufacturers can also look at the role of data in every aspect of their operations.
In this article we discuss how manufacturers integrate data from multiple systems and help increase their bottom line.
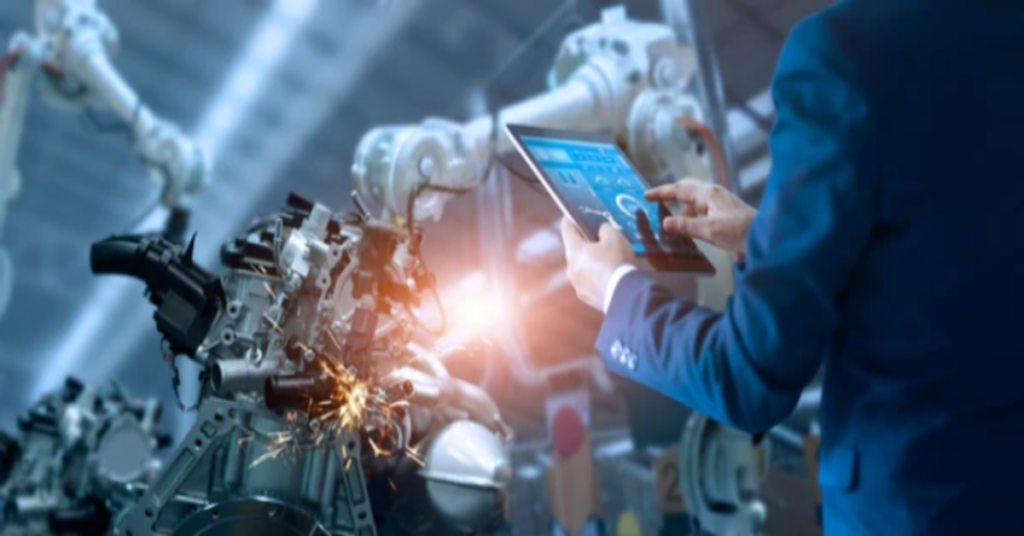
Data, Data Everywhere, and Not a Drop to Exploit!
To understand how data can increase the bottom line, we can begin by asking a lot of questions:
Where does it come from?
Where is it applied?
How do we use it?
How and where do we store it?
How do we analyze it?
Who analyzes it?
Do we have enough data?
Or, do we have too much?

Where Is Your Data Coming From?
Manufacturing data can emanate from numerous sources, both internal and external.
Internal Data Sources
Every report generated in every department – finance, operations, sales, marketing, HR … - contains current data potentially useful as a window into a manufacturer's ongoing business. Historical data reveals positive and negative trends that can guide present and future business decisions.
And then, a variety of sensors have become ubiquitous in many manufacturing environments. Sensor technology plays an essential role in machine automation. Sensors provide information about products during the manufacturing process. They deliver updates about the condition of the equipment. These sensors guide maintenance and prevent downtime. In other scenarios, sensors provide feedback on the motion of the motor to ensure accurate positioning.
If BI (Business Intelligence), AI (Artificial Intelligence), and ML (Machine Learning) technologies are in use, they will provide a treasure trove of additional data.

External Data Sources
The IoT (Internet of Things) and IIoT (Industrial Internet of Things) are significant external data sources. IIoT devices acquire and analyze data from connected assets, locations, and people. They provide insights that can be used to speed the manufacturing process, predict failures, reduce downtime, and increase automation.
The first step is to get hold of the data. The second step is to use it wisely. This can be accomplished by finding relationships in the data to determine cause and effect and improve efficiency and predictability. The ultimate goal is to bring computing to these data streams to shorten decision times, lower expenses, and, wherever possible, eliminate risk.Â
Integrate Data from Multiple Systems, Increase the Bottom Line
Think about all the data sources discussed above, just the tip of the iceberg. Individual, standalone data points are of minimal use. When integrated from multiple systems and sources, these data points can yield actionable results.
Think, for example, about triangulation. If you were to try and determine where a particular cell phone call had been made, you could only do so, with any hope of success, via triangulation. Using cell tower triangulation (3 towers), it is possible to determine a phone location within an area of less than a square mile.
Multiple data points, at least 3, are required. A single data point may be an aberration. Two data points provide only a linear conclusion. The third data point provides greater dimensions.
Let's talk about how manufacturers integrate data…
… and how to use it to your advantage, how manufactures integrate data from multiple systems in ways that can increase your bottom line.
Contact Liberty Grove Software by calling 630-858-7388 or emailing nav@libertygrove.com.
Related Post
Learn About Why a Practical Shop Floor Data Collection Solution is Needed