Dynamics NAV 2013 Assembly Management Part 1 – Overview
About This Post
This is an introductory post to the new assembly management functionality in Dynamics NAV 2013. It is designed to provide readers with a basic overview of this new functionality. Additional posts on more specific assembly management processes and setup issues will follow.
Dynamics NAV Assembly Managment 101
Assembly management will likely be of significant interest to you if your company does one or both of the following:
- You combine items to sell as kits, such as a Christmas basket, which customers can customize when they order.
- You make products by using light manufacturing processes (for example, assembling pre-made furniture) that do not require Dynamic NAV’s full manufacturing capabilities.
Assembling items as kits offers numerous advantages:
- You can accommodate last-minute customer requests.
- You can reduce inventory by stocking core components and then assembling the finished goods only when they’re needed, instead of trying to stock all possible variations of finished goods in advance.
- You can offer special pricing on specific kits, which may assist you in promotional campaigns.
The use of light manufacturing raises an important cost issue: if all you’re doing is performing a simple assembly operation, do you really want to use a full-scale production system that was designed for more complex and demanding tasks? Do you want to pay the cost of buying, setting up, and maintaining NAV’s full manufacturing functionality when you will only use a small fraction of it?
Traditionally, Dynamics NAV addressed these requirements through its kitting functionality. But the old kitting solution piggybacked manufacturing functionality, which meant you still had to pay for unneeded capabilities. Besides, piggyback solutions rarely make for a perfect fit. In the case of kitting, key limitations included:
- An inability to accommodate the true complexity of assembled products, which might consist of a combination of purchased items, manufactured items, and other assembled items.
- Insufficient support for order processors. For example, the sales order interface did not allow the customization, information on component availability, and order promising capabilities required during order entry.
- An inability to combine assembly items in stock and assemble-to-order items on the same sales line.
Dynamics NAV’s new assembly management functionality has been designed and coded from the ground up. It features true assembly items with no dependence on manufacturing, and an assembly order document that is as well-designed and fully featured as NAV’s sales, purchase, and production order documents.
It’s most redeeming quality, however, is the ease with which it handles multiple assembly scenarios, from a simple assembly to fully customized combination orders that require production and purchasing support for successful fulfillment.
Simple Assembly Order Scenario
Make sure you are working from the clean sample database for CRONUS International Ltd. that installs with NAV 2013. In this sample database, item 1984-W is described as “Sarajevo Whiteboard, blue”. It consists of item 1996-S, “ATLANTA Whiteboard, base”, and item 70102, which is a can of blue paint. This composition is recorded in Dynamics NAV 2013’s new Assembly BOM, shown here:
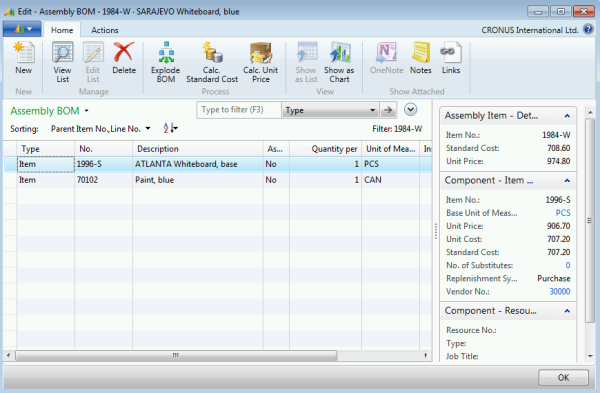
The Assembly BOM page is accessed from the Navigate tab of the item card. It allows you to define the component items, resources, and instructions required to complete the assembly, but, for now, pretend you are dealing with the assembly scenario shown above – the simple combination of two items.
As a salable item that has an Assembly BOM, item 1984-W is already technically an assembly item. However, if you want the sales order interface and the planning system to treat item 1984-W as an assemble-to-order item, you also need to open its item card and set its replenishment system to “Assembly”, and its Assembly Policy to “Assemble-to-Order”, as shown below:
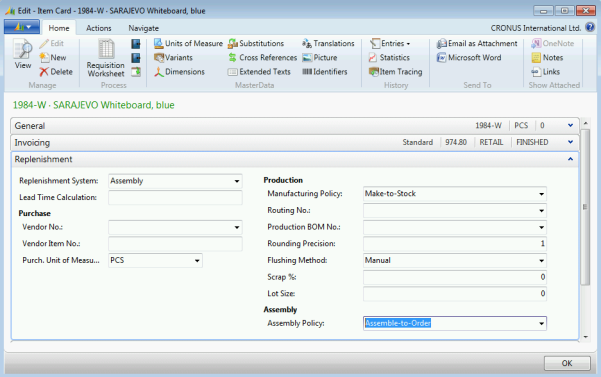
Before you begin, use the item journal to add 5 units of each of the component items 1996-S and 70102 to inventory without specifying a location.
Now create a new sales order for 5 units of item 1984-W for customer 20000 with a requested delivery date of February 05, 2014. Enter the order exactly as you would a sales order for any item, and ignore any credit warnings. When you enter a value in of “5” in the Quantity field of the sales order line, notice that the program immediately populates the Qty. to Assemble to Order and Reserved Quantity fields, as shown below:
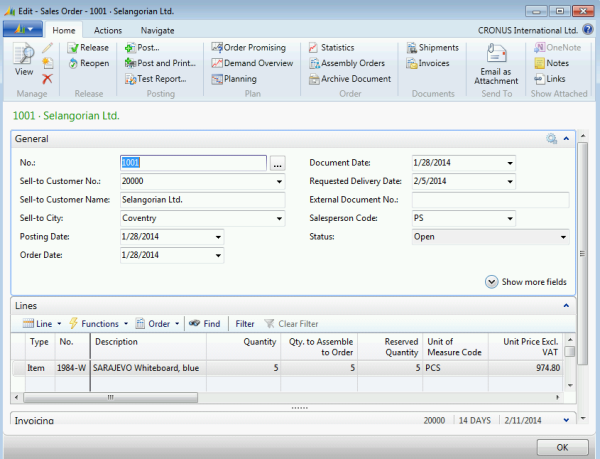
Now drill down into the Qty. to Assemble to Order field. This brings up the Assemble-to-Order Lines page, shown here:
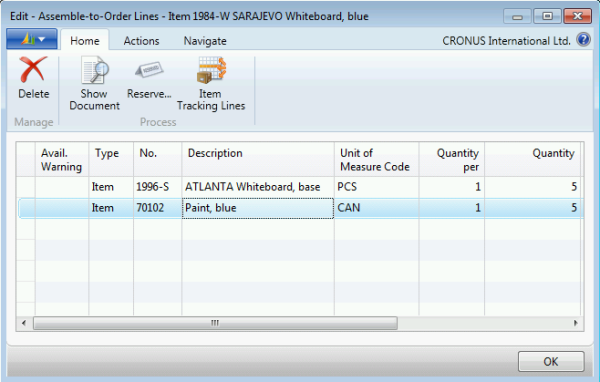
On this page, you can add, delete, or change the items that make up this assembly item. For example, you can change the paint from blue to red. Or you can change the Quantity per value for individual items. This is the page you would use to quickly customize a customer’s order during order entry. I’ll be describing various approaches to support this assembly customization in a later post, but, for now, click the Show Document function on the Home tab. This brings up the actual assembly order, as shown below:
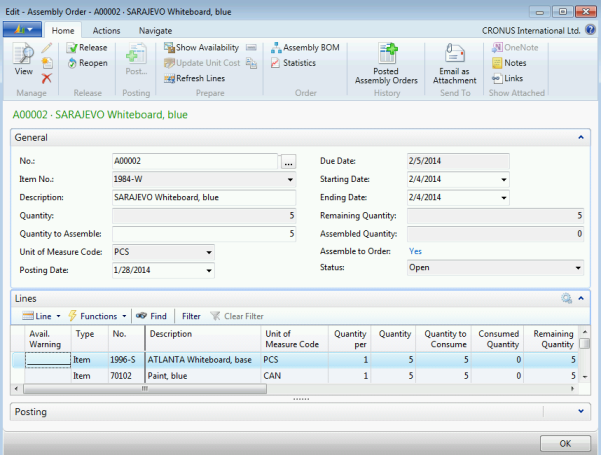
What’s significant about this? Because this assembly order, which was created by the program on your behalf (recall that you did nothing other than simply enter a sales order), is a full-fledged NAV document, complete with its own dimensions, posting functions, associated ledger entries, costing information, and statistics. It also facilitates order tracking, reservations, and warehouse movement/picking. In fact, assembly orders stand at the center of the new assembly management system, and it is this separate and fully defined entity that makes it possible for assembly management to integrate so completely with the rest of the supply system. Indeed, assembly orders now participate in the Dynamic NAV’s supply chain every bit as much as production, purchase, and transfer orders.
At the same time, NAV’s design team never forgot that, while they needed a sophisticated underlying design to achieve such integration, it was equally important to support sales order processors in their interaction with customers. That’s why so much of the interaction between sales orders and assembly orders is automated. For example, escape back to the sales order and reduce the sales quantity from 5 units to 4.
Notice what happens? The Qty. to Assemble to Order field automatically reduces from 5 units to 4, and the underlying assembly order is automatically modified to match.
Drill down into the Reserved Quantity field on the sales order line.
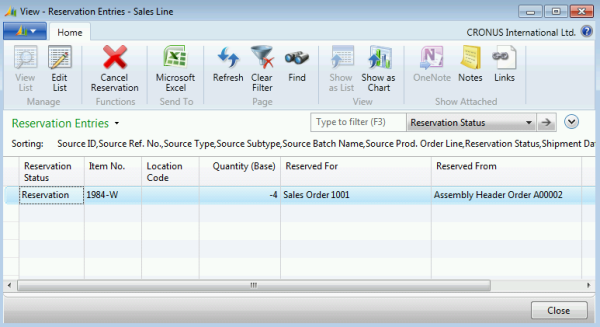
Reservations are also automatically created and maintained.
You can also automatically create inventory movements to move components from their respective bins to the assembly area. From that point on, warehousing functionality takes care of the rest, which means that order processors are asked to do only what they should in the assemble-to-order process: enter the customer’s order as requested.
To complete this post, change the sales order line quantity back to 5 and then ship and invoice the order.
Future Posts In This Series
In future posts in this series, we’ll examine the following basic subjects:
- Assembly order promising
- Planning for assembly items
- Shipping assembly items
- Combination orders and partial shipments
With those basics covered, we’ll then examine a few different assembly order scenarios and discuss the best way to configure Dynamics NAV’s assembly management functionality to address those scenarios.