Dynamics NAV 2013 Assembly Management Part 2 – Order Promising
About This Post
This post describes how Microsoft Dynamics NAV 2013 addresses the challenging tasks of determining the availability of components for assemble-to-order items. It also describes how to promise accurate delivery dates to customers when one or more components are not available until after the sales order due date. For an introduction to assembly management in NAV 2013, see Dynamics NAV 2013 Assembly Management Part 1 – Overview.
Sales Order Entry for Assemble-to-Order Items
You work for a company that makes modular desks, cabinets, chairs, and other business office furniture. Because customer requirements can vary significantly, your company has made the very wise decision to stock main components instead of finished goods, and to rely on assembly management to meet end customer requests.
This sounds like a great idea in the boardroom, but as the sales order processor, you have legitimate concerns. You know that many of your office furniture sets consist of dozens of components, some of which are themselves assembly or production items (multilevel BOM scenarios). Because the finished goods must be assembled from these components, the question of product availability is really a question of component availability. The problem is, how can you check the availability of so many components while speaking to an impatient customer on the phone?
Fortunately, Dynamics NAV 2013 has an answer for that…
Assembly Availability Warning
In the first part of this series, you created a sales order for 5 units of the assemble-to-order item 1984-W, “Sarajevo Whiteboard, blue”, after you ensured that there was sufficient component inventory to make those 5 units. As a result, you did not encounter an assembly availability warning.
This time, create a sales order for 10 units of item 1984-W for customer 20000, with a requested delivery date of February 10, 2014 (ignore the credit warnings). Before entering the Quantity on the sales order line, change the location code for the sales line to SILVER.
Assuming that you have not changed the database since the first post in this series of articles, you should see the following warning page:
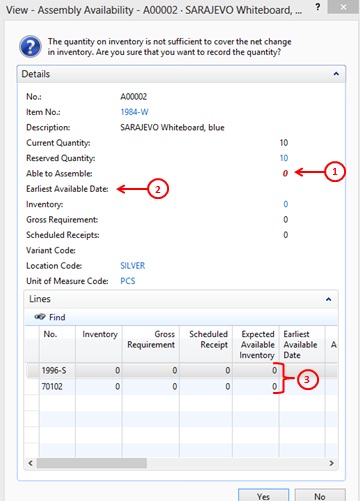
In this case, ignore fields like Current Quantity, Reserved Quantity, Inventory, Gross Requirements, and Scheduled Receipts on the Details FastTab. These all pertain to the finished good item, and in most assemble-to-order scenarios, you won’t have any finished goods items (though you may have a few in inventory from a sales return).
The more interesting fields pertain to components. The most interesting of these is the Able to Assemble field on the Details FastTab (indicated by the red-circled 1). It says “0” in red. Unfortunately for you, this means you don’t have enough components to assemble any 1984-W finished goods.
Red circle # 2 points at a field called Earliest Available Date. This field normally indicates the earliest available date at which your entire sales order line can be fulfilled based on scheduled inbound supply. If no date is displayed, this means that your current inbound supply is insufficient to cover all of your requirements. In short, if you take no additional actions, you will never be able to fulfill your sales order line.
The lines in the Lines FastTab (red circle 3) show you the details for each individual component. In this case, the details are rather straightforward. There is no existing inventory and no scheduled inbound supply for either component. If you scroll to the right, the situation for each component is stated even more clearly in its respective Able to Assemble and Earliest Available Date fields.
Click Yes to proceed despite this warning. Close the sales order, and then do the following:
- Create a purchase order to vendor 10000 for 7 units of item 1996-S, location SILVER, with an expected receipt date of February 15, 2014, and for 3 units of item 70102, location SILVER, with an expected receipt date of February 17, 2014. Close the purchase order.
- Reopen your sales order and re-enter the quantity of 10 in the Quantity field for the sales order line. This results in the following availability warning:
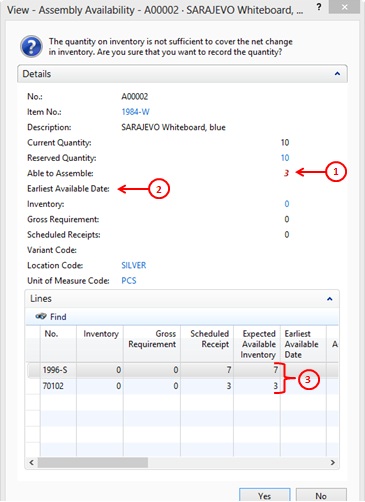
Now the Details FastTab indicates that you can make 3 of the finished goods item 1984-W. Why 3? Because you only have 3 units of item 70102, i.e. it’s your bottleneck. This is easy to calculate because each unit of item 1984-W requires 1 unit of item 70102. If the math gets more complicated, just scroll right and NAV will tell you exactly how many finished goods items you can make per component in the component’s Able to Assemble field.
At this point, there is still no date in the Earliest Available Date field on the Details FastTab because you still can’t completely satisfy the sales order line. To remedy this, open the purchase order you created earlier and increase the order quantity for each component to 12. Make sure that the expected receipt dates remain February 15, 2014 for item 1996-S and February 17, 2014 for item 70102. Then return to sales order and again re-enter the quantity of 10 in the sales order line. This results in the following availability warning.
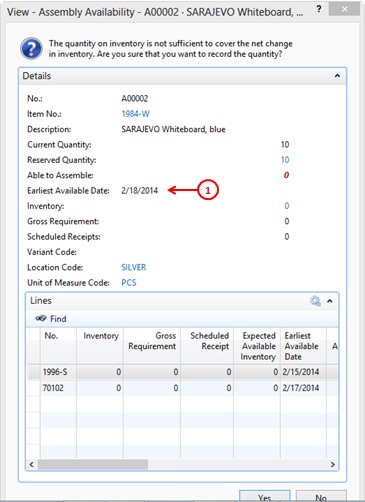
Now there is a date populated in the Earliest Available Date field on the Details FastTab. This is the date that you can promise to your customer.
As you can see from the earliest available dates shown for the individual components on the Lines FastTab, February 18, 2014 is the day after the earliest available date when you will receive the last of the components required to fill your sales line – in this case, component item 70102.
As you can can also see, the warning stops showing quantities for the components once it determines that the sales line can be satisfied at some future date. I don’t know if this is a bug or a design decision, but I find it a bit of a disappointment. I prefer seeing the numbers even after the computer figures out a solution, but perhaps that’s just me.
In any event, you can get that information easily enough. Click Yes to close the warning, and then click Line->Item Availability->BOM Level. This opens the Item Availability by BOM Level page. On the Home tab of this page, click the Expand All function.
In the Option section, set the Demand Date to February 28, 2014, so you can see the bigger picture. Then select the line for item 1996-S and click Event on the Navigate tab. This opens the Item Availability by Event page. On the Home tab of this page, click Expand All and you’ll see the following:
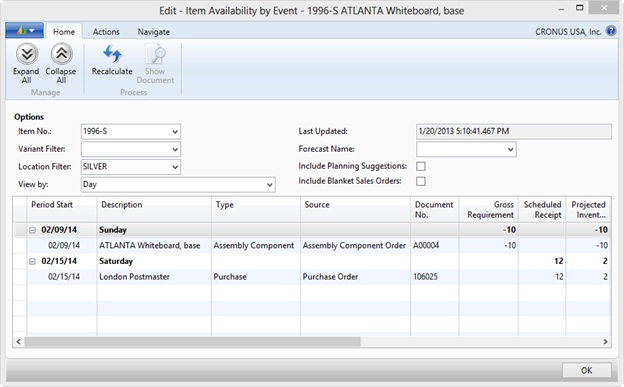
You can’t ask for a much clearer chronological picture than that. Personally, I’d like to see this functionality available directly from the Assembly Availability warning, but, then again, I’d like to be young, handsome, and rich, too.
One last point. The scenarios in this post have been kept simple so as to not obscure the main points, but the value of these availability warnings and pages rises dramatically as assembly items become more complex. Don’t believe me? Item 766BC-B, CONTOSO Office System, has a multilevel assembly BOM consisting of nearly 40 components in total. Try entering a large assembly order for that item (i.e. one that triggers component shortages) without using the availability warning/pages, and then tell me how you feel.