How a Modern ERP Helps Food and Beverage Manufacturers with Traceability and Recall
You've seen the stats. And you understand why Food and Beverage traceability and recall processes are essential for every manufacturer in the sector. It's a no-brainer. Traceability and recall management are two of the most critical aspects of food safety today. However, ensuring your manufacturing facility meets compliance requirements and has effective traceability and recall processes can be daunting.
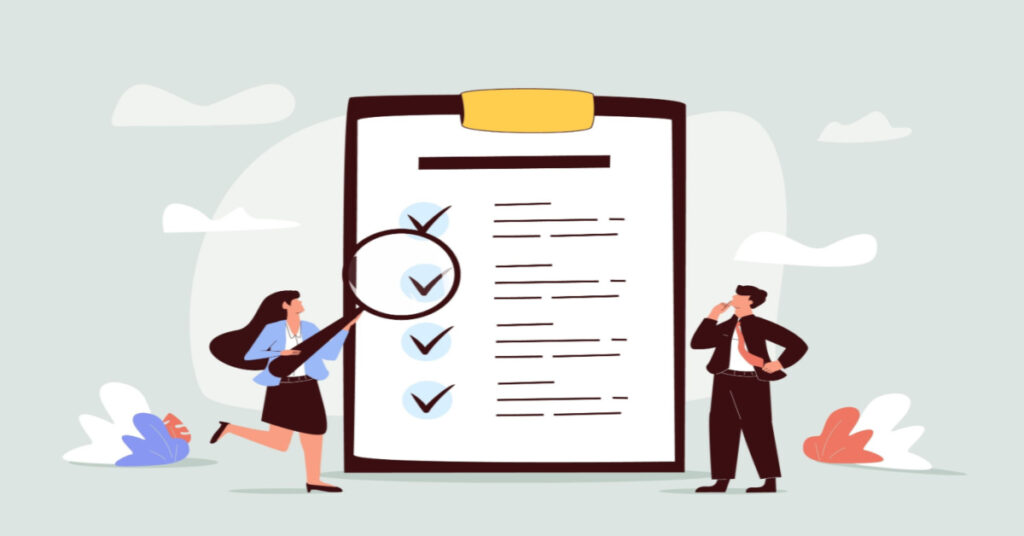
That's where a modern, cloud-based ERP (Enterprise Resource Planning) system, such as DynamicsFoodERP from Liberty Grove, powered by Microsoft Dynamics 365, can assist manufacturers in improving product safety, managing recalls and traceability, and protecting their reputation.
Food and Beverage ERP software can enable detailed product tracking and tracing and handle the recall process, assisting Food and Beverage manufacturers in protecting their customers and businesses. Integrated software can track products at the lot and serial level and help execute a comprehensive recall in minutes by being able to trace products throughout the supply chain.
The Importance of Traceability Management
Traceability refers to tracking and tracing items and their components from raw materials to final goods. This functionality is critical for several reasons:
- Ensuring product safety and quality
- Meeting regulatory guidelines
- Lowering the likelihood of product recalls
- Facilitating timely and efficient recalls when necessary
- Safeguarding the company's brand and consumer trust
Recall Management Challenges
Product recalls are a common occurrence in the manufacturing business. They can be expensive, time-consuming, and detrimental to a company's reputation. Food and Beverage manufacturing managers must:
- Identify the fundamental cause of the problem
- Locate damaged items in the supply chain
- Communicate with customers and stakeholders
- Manage the logistics of product returns and replacements
DynamicsFoodERP software can assist manufacturers in overcoming these obstacles and improving traceability and recall management processes, reducing the recall's cost and reputational impact.
Food and Beverage ERP Software's Role in Traceability and Recall Management
Improved Visibility and Control: Food and Beverage ERP Software provides a centralized system through which businesses can manage all operations, from procurement to manufacturing to inventory management and distribution. That gives Food and Beverage managers more insight and control over the whole supply chain, allowing them to detect and fix issues swiftly, assure product safety and quality, and comply with regulatory requirements.
Better Data Management and Reporting: Modern ERP software enables businesses to collect, store, and analyze massive amounts of data from diverse sources. It contains raw materials, manufacturing procedures, product testing, and shipment data. Food and Beverage manufacturers can provide accurate and timely reports by combining this data into a single system, enabling speedy decision-making and effective recall management.
Simplified Recall Management Processes: Food and Beverage ERP Software automates many components of the recall management process, decreasing the time and effort needed to carry out a recall. It includes identifying concerned products, alerting customers, processing product returns and replacements, and tracking the recall's progress. It also assists manufacturers in keeping detailed records of their recall actions, assuring regulatory compliance.
An industry-specific Food and Beverage ERP system aids in tracing and recall by ensuring total traceability of raw materials and final goods throughout the supply chain. It's significant since many countries, like the United States and Europe, require it by law. ERP solutions can also make issuing and carrying out a recall easier and faster.
Case Study
XYZ Foods, a manufacturer of popular frozen foods, had to recall an entire batch of chicken nuggets due to potential salmonella contamination. Initiated after several customers reported feeling ill after consuming the product, the recall resulted in a loss of USD 4.6 million in revenue and a significant dent in the company's reputation.
After the recall, XYZ Foods realized that it needed to improve its food traceability and recall processes to avoid future recall issues and protect its reputation and the safety of its customers.
The management team selected DynamicsFoodERP from Liberty Grove, powered by Microsoft Dynamics 365. This modern, cloud-based ERP system helped XYZ Foods track and trace raw food materials and finished products throughout the supply chain. It also made issuing and executing a recall much easier and faster. The system ensured total traceability of raw materials and identification of the source of contamination, should it be identified in production facilities or further downstream. The ERP system also enabled XYZ Foods to comply with regulatory requirements regarding traceability and avoid mistakes that could result in a recall.
After implementing the ERP system, XYZ Foods improved its food traceability and recall processes, which helped the manufacturer avoid future recall issues. The ERP system enabled XYZ Foods to gain better visibility into its supply chain and make informed decisions about its operations. It also reduces the cost of recalls, should they occur, and improves the company's bottom line.Â
Overall, implementing the DynamicsFoodERP was a success for XYZ Foods and helped the organization achieve its business goals
.
ERP Software Advantages for Traceability and Recall Management
Quicker Issue Resolution: Food and Beverage ERP software enables manufacturers to identify and respond to issues that may jeopardize product safety and quality. By streamlining the recall management process, businesses can shorten the time necessary to execute a recall, limiting their firm's financial and reputational damage.
Reduced Recall Risk: ERP software helps firms reduce the risk of product recalls by boosting supply chain visibility and control, improving data management and reporting, and using advanced technologies such as BI and RPA. It safeguards the company's reputation and saves time and resources on recall management.
Improved Regulatory Compliance: Food and Beverage ERP software assists businesses in keeping detailed records of their traceability and recall management processes, assuring regulatory compliance. By automating several components of the recall process, the program decreases the possibility of compliance violations caused by human mistakes.
Increased Customer Trust: Maintaining customer trust in the Food and Beverage manufacturing industry requires effective traceability and recall management. By investing in modern ERP software, businesses can demonstrate their dedication to product safety and quality while strengthening their connections with consumers and stakeholders.
Best Practices for Implementing a Modern Food and Beverage ERP Software Solution
Choosing the right Food and Beverage ERP Solution: ERP software is different. Selecting a system that suits your company's specific demands and specifications, such as traceability and recall management capabilities, is critical. Vital considerations include scalability, ease of interaction with current systems, and the availability of technical support and training resources.
Involve stakeholders in the deployment process: Successful ERP deployment necessitates the participation and commitment of stakeholders from all company levels. It involves procurement, production, quality control, logistics, and other traceability and recall management departments. Engage these stakeholders in the ERP system's planning, deployment, and continuing management to ensure its success.
Invest in training and adjustment management: Implementing a new ERP system can substantially adjust staff. Therefore, sufficient training and support are required to achieve successful adoption. It includes technical software training and change management initiatives to help staff comprehend the new system's benefits and how it will affect their regular tasks.
Continuously monitor and optimize the system: As with any technology investment, ongoing monitoring and optimization are critical to ensuring that your ERP system continues to meet your company's traceability and recall management requirements. Review system performance regularly, identify areas for improvement, and make required changes to optimize the system for optimum efficiency and effectiveness.
Conclusion
Traceability and recall management are critical to product security in the Food and Beverage manufacturing industry. A cloud-based ERP solution can assist businesses in improving their traceability and recall management procedures by utilizing sophisticated technologies such as Business Intelligence, Robotic Process Automation, Mobile Applications, and the Internet of Things.
By investing in a modern ERP solution, Food and Beverage manufacturers can improve product safety, minimize the risk of recalls, comply with regulatory standards, and preserve customer trust in a competitive market.
DynamicsFoodERP provides a complete traceability system that allows manufacturers to track materials from receipt to delivery, quickly identify, quarantine, and retrieve potentially defective goods, accelerate the time to completion of product recalls, improve governance and drive compliance, continuously test and improve traceability systems, remain compliant and meet regulatory reporting requirements, and mitigate the risks associated with recalls.
Is Your Food and Beverage Operation Protected by a Modern ERP Solution?
Liberty Grove can help you use many tools and services to help you achieve a successful Food and Beverage Cloud ERP deployment that will improve your organization's ability to trace and recall products should the need arise.
Contact Liberty Grove for a complimentary consultation on how DynamicsFoodERP can help you through a smooth Cloud ERP deployment and give you the data insights you need to protect your reputation.
Related reading:
Food Traceability | How Cloud ERP Can Help (libertygrove.com)
Compliance Matters: 8 Ways ERP Can Help Food and Beverage Manufacturers (libertygrove.com)
Best 10 Reasons to Move Your On-Premises ERP to the Cloud - Liberty Grove Software
About the author
Liberty Grove Software is an established Microsoft Partner that focuses on providing customers with sales, service, and support for Microsoft Dynamics 365 Business Central/NAV solutions and training and upgrades.
Over more than 25 years, Liberty Grove has assisted hundreds of customers with businesses ranging from small to mid-sized to Microsoft Partners in implementing, training, customization, and upgrading Microsoft Dynamics ERP solutions.
The organization is one of only a few companies worldwide that Microsoft recognizes as qualified to provide Business Central/NAV Upgrade Service Centers.