Checklist: Streamline Your Food Business and Boost Confidence with a ERP Solution for Recall and Traceability Compliance
CDC estimates that roughly 1 in 6 Americans (or 48 million people) get sick yearly, 128,000 are hospitalized, and 3,000 die of foodborne diseases. (Burden of Foodborne Illness: Findings | Estimates of Foodborne Illness | CDC)
That's a food manufacturer's nightmare.
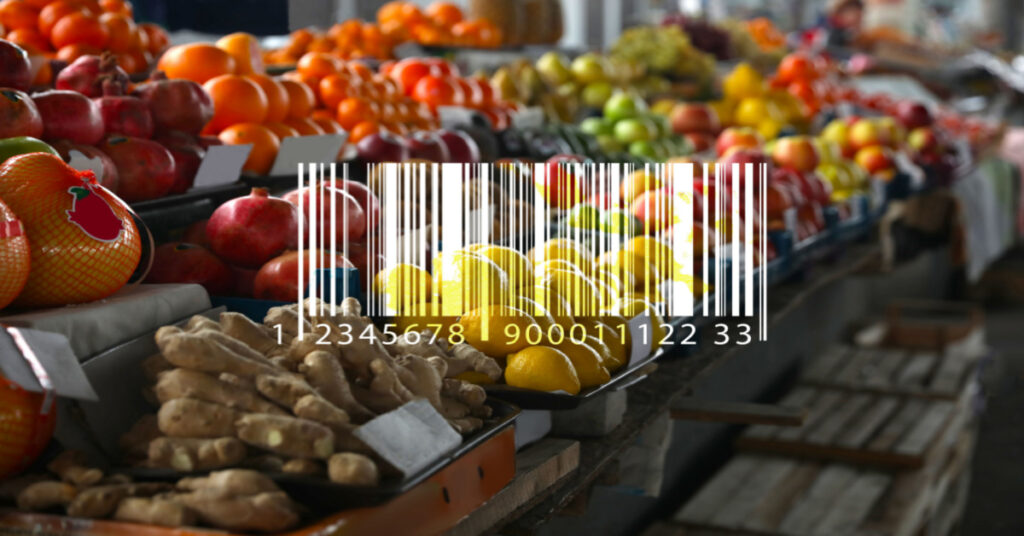
Recalls occur. Often, the problem is beyond your control. In a recall emergency, it can be challenging to know what to do and in what order to expedite the recall process with as little friction as possible.
If you're using an ERP solution, you're already ahead of the situation. Many tools you'll need for recalling goods are already available within your ERP.
This checklist has two sections:Â
Section 1: What to consider before a recall occurs
- Planning for the worst-case scenario ensures preparedness for what you hope will never happen. That's where your ERP comes in – it's your recall assistant.
Section 2: Step-by-step procedures to work through the recall process
- When the unthinkable happens, being prepared enables swift team action and helps maintain customer confidence – and your brand reputation.
Part I: Getting Ready
- Establish a Documented Recall Team
Those responsible for decision-making, quality assurance/technical advisory, media communication, complaint investigation, contacting accounts, government contact, and legal counsel.
- Complaint Form
While you may only need this once a recall occurs, preparation is a good idea. The complaint file has three sections:
• Documentation of the initial complaint information
• Investigation of the complaint and documentation of the findings
• Acting on the findings of the investigation
- Quick Information Access
An ERP solution enables quick access to critical information about products, manufacturing processes, the location of items in the supply chain, and contact information for those during a product recall.
- Capability to Find Any Item in the Supply Chain
Throughout the supply chain, an ERP solution (along with barcodes and RFID) enables traceability down to specific ingredients. Connect production and quality management testing to determine which other products may pose a risk due to cross-contamination or faulty processes.
- Actionable Communication Transparency and Openness
Open communication with suppliers, customers, and government agencies helps mitigate the impact of a food product recall. ERP users can quickly email documents, alerts, instructions (such as how/where to dispose of products, etc.), and updates to contacts in bulk or individually from the software's interface. When a faster recall is required, manufacturers can temporarily open access to product location information by authorizing external users, such as suppliers or customers, to access and pull data from their systems.
Contact your Food Inspection Agency immediately if you suspect you sold an unsafe or illegal food product to another manufacturer, distributor, or retailer.
Part II: Plan of Action
- Engage the Recall Management Team
- Inform the Food Inspection Agency
- Identify all products in the recall
- Detain and segregate all recalled products under your company's control
- Create a Press Release (if required)
- Make a Distribution List
- Prepare and distribute the Recall Notice
- Check the recall's effectiveness
- Control the recalled item(s)
- Decide what to do with the recalled product(s)
- If the recall occurred at your facility, resolve the issue
Quickly tracking and removing defective problems with clear communications can significantly mitigate a product recall's financial and brand reputational consequences. A company with the tools and procedures for a covert recall shows its customers and supply chain partners that it values its relationships.
Customers judge a company on how well it prepared for a recall and how it responded when things went wrong.
Be prepared.
About the author
Liberty Grove Software is an established Microsoft Partner that focuses on providing customers with sales, service, and support for Microsoft Dynamics 365 Business Central/NAV solutions and training and upgrades.
Over more than 25 years, Liberty Grove has assisted hundreds of customers with businesses ranging from small to mid-sized to Microsoft Partners in implementing, training, customization, and upgrading Microsoft Dynamics ERP solutions.
The organization is one of only a few companies worldwide that Microsoft recognizes as qualified to provide Business Central/NAV Upgrade Service Centers.