Learn About Why a Practical Shop Floor Data Collection Solution is Needed
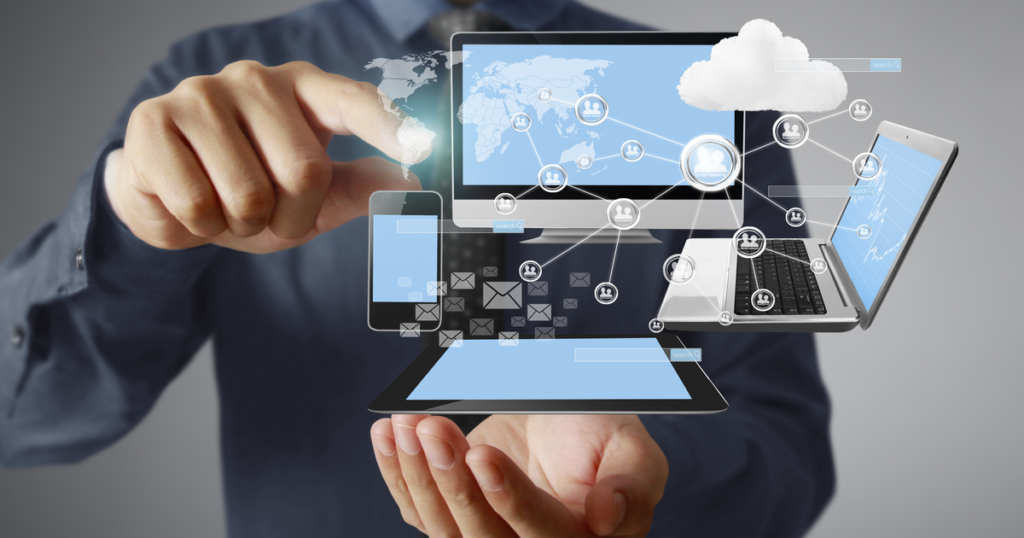
You can’t escape it. The unprecedented amount of data bombards you day and night, day in and day out. It’s a never-ending stream. Before establishing a practical shop floor data collection system, you must determine what data is essential for your business and what data is unimportant, merely a distraction.
Whether it’s data generated internally, data manually entered into your system, data from sensors, or data from the IIoT (Industrial Internet of Things), take a breath and decide what to keep and what to discard. Only then can you set up a shop floor data collection system that makes sense. Only then will your data collection system become practical.
The Benefits of a Practical Shop Floor Data Collection System: Your Data Tells a Story!
A practical shop floor data collection program will digitally transform your factory, allowing you to make data-driven decisions that will improve productivity based on real-time information, machine monitoring, and benchmark analysis.
You will gain real-time visibility with apps that collect data from the people, machines, and sensors throughout your operations. You will be able to optimize production by identifying and solving bottlenecks in real-time.
You will be able to calculate cycle time and first-pass yield data for a complete picture of your operation’s productivity. You will be able to minimize downtime by properly balancing work across stations.
You will uncover opportunities to improve operations along your production line. You will be able to build triggers and time-saving workflows by incorporating events and measurements recorded by devices and sensors. You will have the traceability you need for accountability.
You will be able to resolve issues and be proactive based on data, not guesswork.
Say Good-Bye to Manual Tracking
At Liberty Grove Software, the solution we recommend and offer our manufacturing clients is Shop Floor Insight, a Manufacturing Execution System (MES) add-on for Microsoft Dynamics 365 Business Central that significantly reduces the labor costs and errors associated with manual data entry. Shop Floor Insight allows employees to use barcode scanners or touch screens to speed up shop data input for time, material, quality, etc.
The numerous benefits of a shop floor data collection system include, but are by no means limited to, the following twelve:
- Eliminate manual time entry with barcode scanning for Production Orders, Jobs, Service Orders, and Fixed Assets
- Capture operational data on the shop floor, including consumption, output, scrap, and quality
- Record and report on non-productive and rework time for better insight into lost productivity
- Record time and attendance based on employee shifts with exception reporting
- Quickly approve time with exception-based supervisor approvals
- Automatically calculate overtime and shift differentials for integration with payroll systems
- Streamline shop floor data capture
- Enhance data capture and management
- Significantly reduce rework
- Analyze job progression and costing
- Maintain a detailed production history
- Immediate notification to supervisors/chain of command
Shop Floor Insight ROI (Return on Investment)
Shop Floor Insight pays for itself in as little as three months. By automating your shop floor data collection, you will increase data accuracy, reduce unnecessary overhead costs, and improve the efficiency of your staff by enabling them to focus on value-added tasks to drive business performance.
The Shop Floor Insight ROI calculator will help you estimate the key financial benefits of the solution:
- How much overhead time can be saved by automating your shop floor data collection
- Savings gained from increased quality
- The increase in sales driven by improved efficiency and quality
- The payback period for Shop Floor Insight
Take the next steps…
Contact Liberty Grove Software by calling 630-858-7388 or emailing nav@libertygrove.com.