7 Ways Food and Beverage ERP Can Help Track Food Quality
When it comes to food and beverage production, quality is king. No food and beverage executive wants the call that says their company's product is under recall. Or worse, that consumers have suffered injurious harm or death because of foodborne illness. That's why food quality is top-of-mind every day for manufacturers.
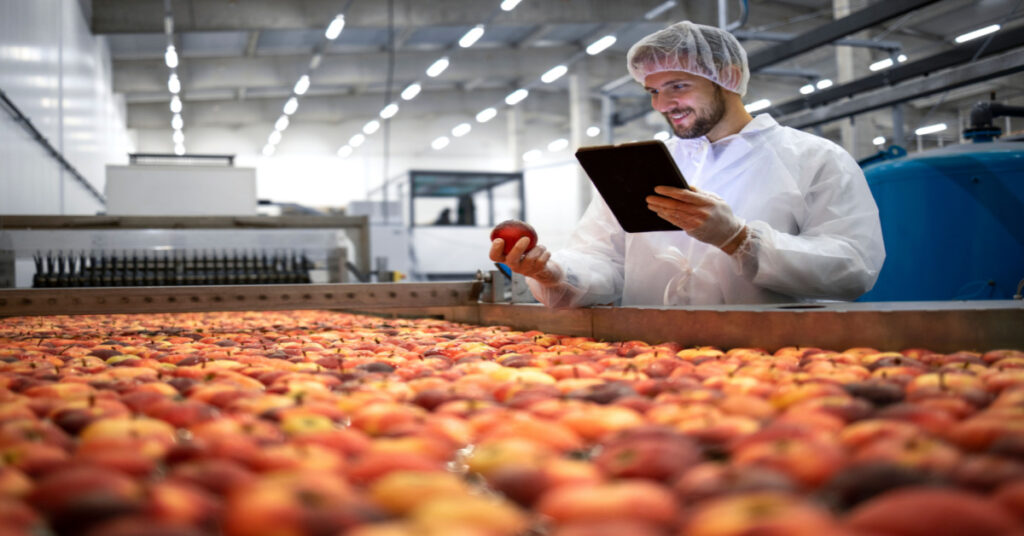
Of course, consumers want to feel confident that the goods they purchase are worth their money. They also want to know that the food they put on the table to feed their families is safe. The only way to ensure their satisfaction is to ensure every product leaving your facility and traveling downstream meets the same high standards you have established.
Better brand recognition and increased profitability are benefits of maintaining continual excellence in quality. After all, it makes sense that consumers will favor your product over others if you can produce a better product than your competitors. However, there are considerable dangers associated with failing to put proper food quality control systems in place, including the potential loss of market share or an emergency involving food safety.
The food and beverage business has several essential quality procedures, and to properly master them all, you'll need technology specifically designed for the job, like an enterprise resource planning (ERP) solution.
So, how can the DynamicsFoodERP system save your bacon?
Let's look at seven strategies for handling food quality control issues and how Liberty Grove Software’s DynamicsFoodERP system can help.
1. Create a list of your authorized suppliers
Your company probably has a few reliable, regular material suppliers, but organizing your approved suppliers by ingredient helps to ensure that you have the best raw materials before the manufacturing process starts. This list should contain the precise name of each ingredient, your internal code or identification, and the contact information for any linked suppliers.
ERP platforms may assist you in collecting all of this data, along with the supplier contracts you sign, and maintaining it digitally in a readily accessible company-wide database. By doing so, you can ensure that everyone knows exactly where your ingredients originate and that you are always making purchases from vendors that have received your approval.
2. Requirements for specific ingredients
The expression "your products are only as good as what you put in them" has become somewhat of a cliché, yet it is true. Depending on the component type, you may need to specify what is acceptable regarding sourcing, shelf life, composition, packaging, country of origin, and purity. It would help if you also made this evident to your suppliers.
By digitally recording this information and making it widely accessible to all parties, food ERP solutions help on this front. Once the items are received and evaluated, your staff will have a clear set of standards to compare their findings against, allowing them to decide if everything is up to par or if a return to the supplier for replacement is required.
3. Carefully manage recipes and formulas
Your product development teams spent much time and effort perfecting the recipes for your food and beverage offerings. When customers choose to repurchase their favorite products, they expect consistency. That makes developing precise formulas and adhering to them essential for your firm.
Nearly all industry-specific ERP platforms for the food industry will include some recipe management features. Still, cutting-edge systems like ERP go one step further by interacting with intelligent manufacturing equipment and importing data from it in real-time. That lets your employees immediately step in and fix any problems if a single item or manufacturing run deviates from the norm.
4. Comply with all applicable laws and good manufacturing practices
The U.S. Food and Drug Administration created Current Good Manufacturing Practices (cGMP) for food and beverage businesses to maximize outcomes and reduce risks in manufacturing, processing, and packaging food and beverage goods. The regulations, which are still a reliable foundation for safe and efficient operations, were included in the Federal Food, Drug, and Cosmetic Act.
It may be beneficial to obtain additional certifications, such as those from the International Organization of Standardization (ISO 22000), the British Retail Consortium Global Standards (BRCGS), the Safe Quality Food Institute (SQFI), the Hazard Analysis and Critical Control Points (HACCP) methodology, and the Foundation Food Safety System Certification 22000 (FSSC 22000). Additionally, you have a legal obligation as an organization to abide by all relevant food safety and compliance requirements, such as those established in the U.S. Food Safety Modernization Act (FSMA), depending on the location of your facilities and in which nations you sell your products.
Food and Beverage ERP solutions assist in enforcing requirements by automatically scheduling checks of your processes and compliance procedures. You can develop a culture of food safety and best practices that will go a long way toward preserving the quality of your products by routinely reviewing your operations, tools, and employee behaviors.
5. Gather and track real-time data on food quality
Ensuring your results meet your expectations requires careful production process monitoring while your lines are operating. Without close attention to what is happening and how your machinery works, you risk wasting materials by using them in products of poor quality. When you need to trash your product, you lose money and harm your enterprise's viability.
However, not all ERP systems are made equal in this regard. ERP systems designed for the food and beverage industry, like DynamicsFoodERP, often include quality management capabilities, making collecting and analyzing in-process quality data easier. The ability of Food & Beverage ERP to integrate with intelligent sensors, scales, and thermometers enables the collection of essential data, including cooking temperature and consistency, as well as color, shape, and other vital aspects. It immediately updates your interface to identify and correct issues proactively.
6. Ascertain appropriate packaging and labeling
Although not directly related to the quality of your products, how finished goods are packaged and labeled can significantly influence how customers feel about them. You must make sure that the secondary packaging (any material that bundles multiple products together) fits the shape and durability of the items inside, all necessary labels are correctly applied, and the primary packaging – i.e., that which comes into direct contact with the product – is appropriate to the type of food or beverage it contains.
Strong packaging and labeling management tools are crucial to food and beverage ERP solutions because of these factors. With the help of these tools, you'll be able to rapidly print the appropriate labels with all the information they need, including nutritional facts, ingredient lists, and allergen declarations, and configure the requirements according to the type of product.
7. Prepare a comprehensive recall plan
As important as taking proactive measures to ensure that products satisfy quality standards, it's equally important to have a plan in place in case something goes wrong and a product withdrawal or recall is required. Regarding food safety situations, there is nothing worse than hustling because time is of the essence. It's especially true given the increased attention that the industry is receiving from both regulatory agencies and consumers.
With extensive traceability features, industry-built ERP systems can assist you in locating faults and tracing the origin of contamination back up the supply chain. Still, they can also automate several steps in the recall procedure, such as sending notifications to affected parties. These technologies give businesses visibility, so you won't have to wonder where the problematic material came from or which items the production team used.
Uncompromising Food Quality: The Right Technology is Required
This list makes it abundantly evident that a production team cannot achieve food quality control by performing a single pass or a cursory examination of several characteristics as products leave the production line. From the moment ingredients enter your facilities until the finished goods leave for their final destinations, it is a complicated process that requires action.
It should also be clear how the correct technology solution can help your company achieve everything necessary. You can free your team from the strain of manual recording processes and eliminate the potential for human error because food ERP solutions can automate quality checks and ensure correct performance every time.
There are many ways in which DynamicsFoodERP, our sector-specific food and beverage solution, excels in quality assurance. There are also many more excellent reasons to choose us for your enterprise software requirements. At Liberty Grove Software, our employees have years of experience in the food and beverage sector.
Because all our solutions are Microsoft Dynamics 365-based, our team has access to all the benefits of the most recent advancements and improvements.
Conclusion
Liberty Grove Software can help companies solidify their market position by ensuring food quality through our DynamicsFoodERP, ensuring food quality and the safety of their products. Because when it comes to food quality, subpar simply isn't good enough.
Contact Liberty Grove Software for a complimentary consultation on implementing the right ERP system to protect your customers, your organization – and your reputation.
Related reading:
Critical Success Factors for the Food Manufacturers (libertygrove.com)
About the author
Liberty Grove Software is an established Microsoft Partner that focuses on providing customers with sales, service, and support for Microsoft Dynamics 365 Business Central/NAV solutions and training and upgrades.
Over more than 25 years, Liberty Grove has assisted hundreds of customers with businesses ranging from small to mid-sized to Microsoft Partners in implementing, training, customization, and upgrading Microsoft Dynamics ERP solutions.
The organization is one of only a few companies worldwide that Microsoft recognizes as qualified to provide Business Central/NAV Upgrade Service Centers.